Masterbatch
Dust-free and efficient coloring material for plastics
Mono masterbatches are colored pellets obtained by dispersing an unusually high amount of pigment uniformly within a resin matrix. Due to the surface characteristics of the pigments, the content of different types of pigments in masterbatches varies. Typically, the mass fraction range for organic pigments can reach 20%-40%, while for inorganic pigments, it is generally between 50%-80%.
During the masterbatch manufacturing process, the pigment particles are well dispersed uniformly within the resin, so when used for plastic coloration, it can exhibit excellent dispersibility, which is the fundamental value of masterbatch products. Additionally, the color performance of masterbatch products is customized according to the final customer's requirements, which means that coloration is one of the two primary functions of masterbatch products.
The main advantages of the masterbatch coloration process are:
● Excellent dispersibility
● Stable quality
● Precise metering
● Simple and convenient batch mixing
● No bridging during feeding
● Simplified production process
● Easy to control, ensuring production efficiency, product quality, and performance stability
● No dust, no contamination to the processing environment and equipment
● Masterbatch products can be stored for an extended period.
Masterbatch products are typically used at a ratio of around 1:50 and are widely used in areas such as films, cables, sheets, pipes, synthetic fibers, and most engineering plastics. It has become the mainstream coloration technology for plastics, accounting for more than 80% of plastic coloration applications.
In addition, additive masterbatches refer to the incorporation of an unusually high amount of functional additives into the resin, resulting in a masterbatch with special functionalities. These additive masterbatches can impart properties such as aging resistance, anti-fogging, anti-static, and others to plastics, thereby expanding the new applications of plastics.
Applications

Thermoplastic

Synthetic Fiber

Film
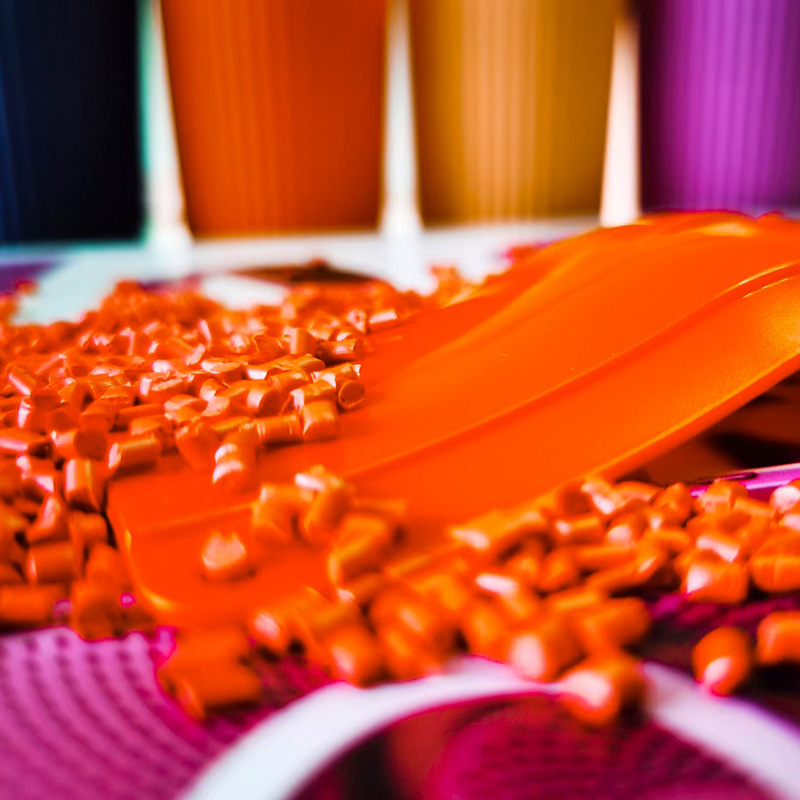
Reise ® mono masterbatch for PE
The Reise mono masterbatch PE carrier based are suiltable for polyethylene applications, such as blow film, cast film, cable and pipe.
The features of this masterbatch group are:
● Smooth film surface, suitable for automatic filling production requirement.
● Comply with food hygiene performance requirements.
● Good heat-sealing properties.
● Certain level of pressure resistance and impact resistance.
● The wetting agent in the masterbatch are mainly polyethylene wax.
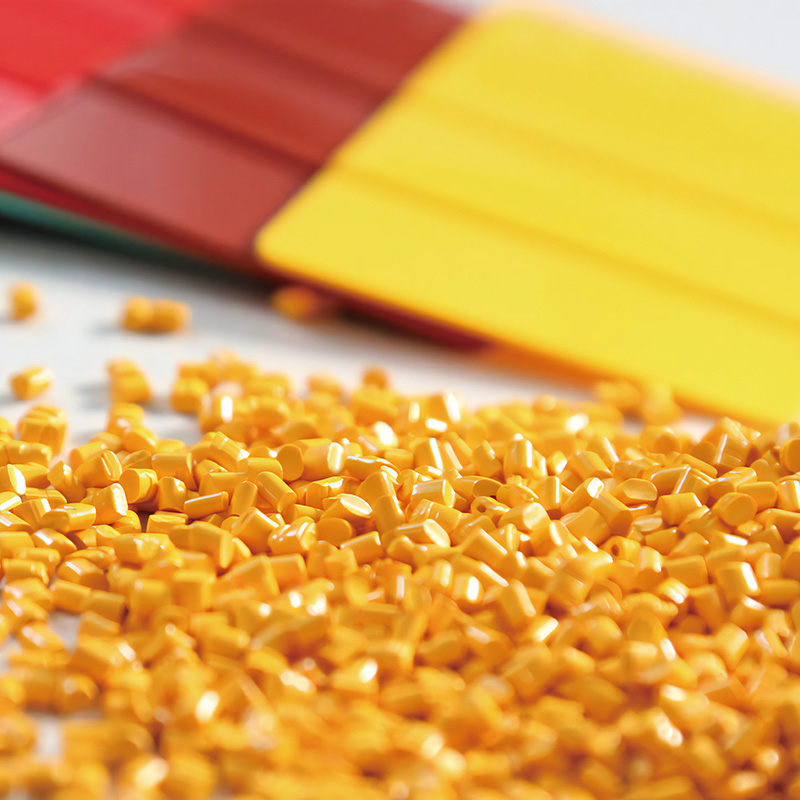
Reise ® mono masterbatch for PP fiber
The Reise mono masterbatches are used for polypropylene fiber.
The Reise mono masterbatches have excellent spinnability, meet the requirements of the spinning pack replacement cycle, have good heat resistance of the pigment, and good migration resistance.
● For the formulation, the titanium dioxide pigment concentration that can reach 70%, the organic pigment content can only reach 40%. If the concentration in the masterbatch is too high, it will be difficult to process and affect the pigment dispersibility. Moreover, polypropylene is used as the carrier, and the compounding temperature is relatively high, so the pigment concentration in the masterbatch is determined based on the customer's requirements and processing conditions.
● Using polypropylene wax can increase the extrusion viscosity, which is beneficial for pigment dispersion.
● It is generally best to use a fiber-grade PP resin (melt flow index 20~30g/10min) and PP resin in powder form.
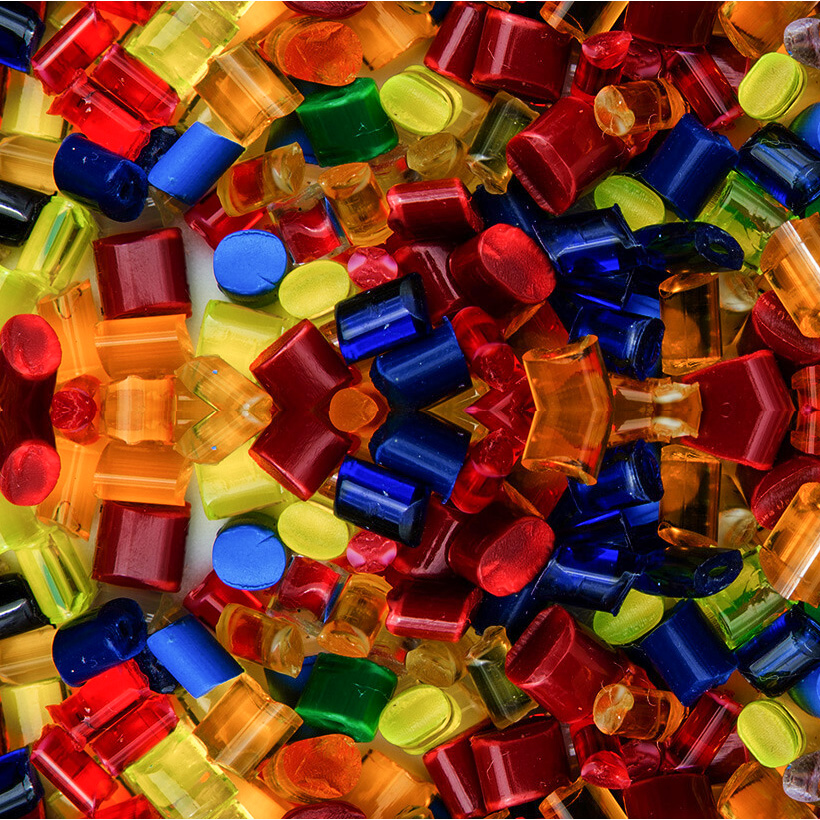
Reisol ® masterbatch for polyester
Reisol® masterbatches can meet the requirements of excellent heat resistance, outstanding dispersibility, and good migration resistance for polyester fiber. They also provide good water resistance, alkali resistance, light fastness, and weathering resistance during the subsequent processing.
The Reisol® masterbatches have below features:
-
● Excellent dispersibility;
-
● Excellent heat resistance;
-
● Excellent migration fastness;
-
● Excellent Acid&Alka resistance.
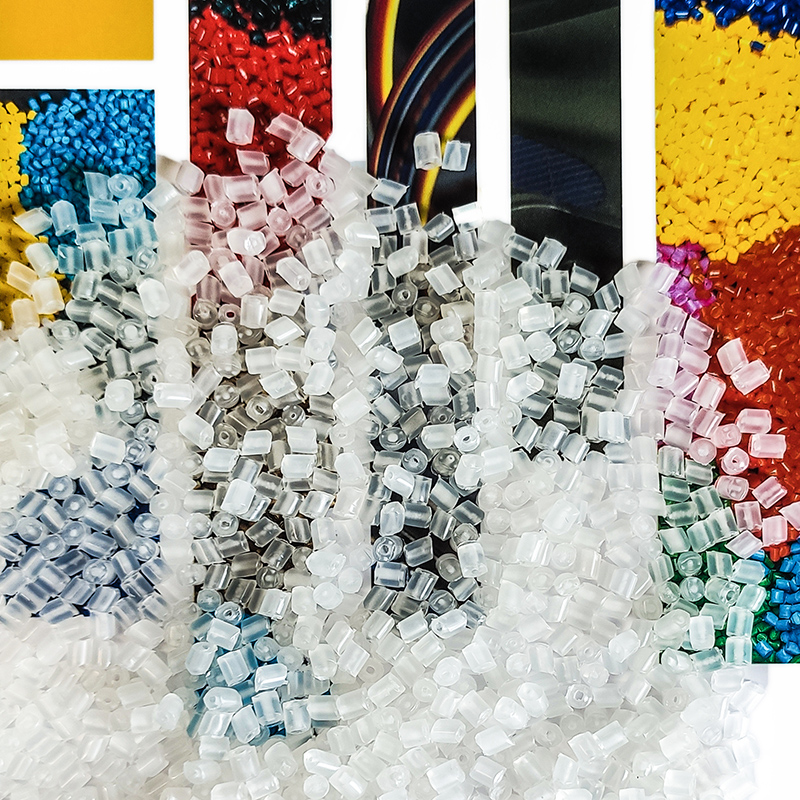
Additive masterbatch
Additive masterbatches contain additives that can impart special effects or improve the performance of plastics (fibers). Some of these additives are used to address specific deficiencies of plastics, while more are used to add new functionalities to plastics, such as extended service life, flame retardancy, anti-static properties, moisture absorption, odor removal, conductivity, antimicrobial properties, and far-infrared effects. Additionally, they can be used to achieve special effects in plastic products.
Additive masterbatches are concentrated formulations of various plastic additives. Some additives have a low melting point, making direct addition difficult to disperse, so they are often added in the form of masterbatches to reduce the cost of plastic products. This is more efficient and helps maintain the desired performance effects.